opening work in process inventory formula
Work-in-process is an asset and so is aggregated into the inventory line item on the balance sheet usually being the smallest of the three main inventory accounts of which the others are raw materials and finished goods. For example you have run out of materials to create a certain amount of products.
Total Manufacturing Costs Beginning WIP Inventory Ending WIP Inventory COGM.
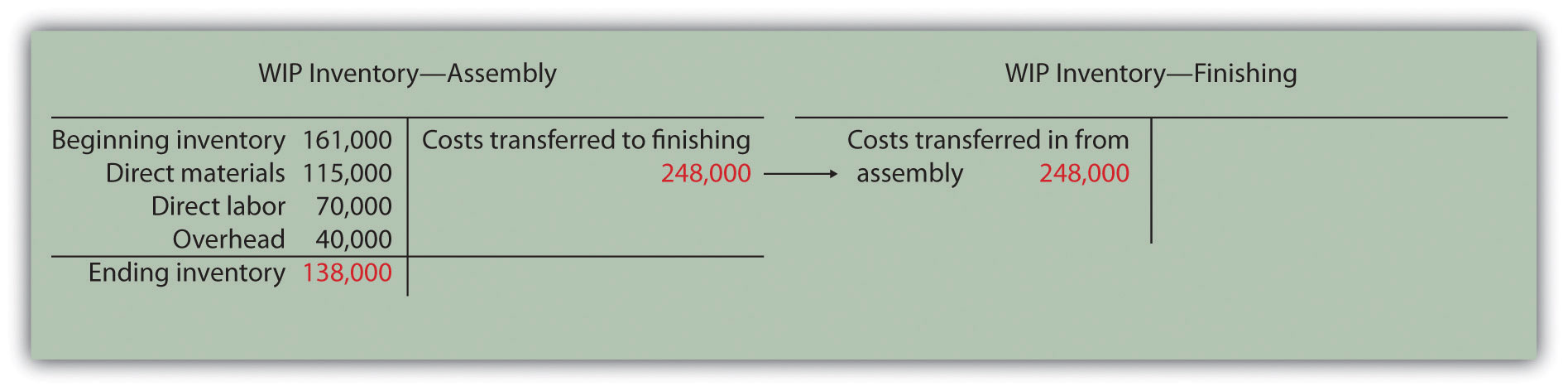
. Imagine BlueCart Coffee Co. This is when the. Opening Inventory Cost of Goods Sold Ending Inventory - Purchases.
Ending inventory Beginning inventory Inventory purchases Cost of goods sold or Ending Inventory Beginning Inventory Inventory Purchases. Formulas to Calculate Work in Process. At that point the inventory is no longer raw.
Related
Ending inventory Previous accounting period beginning inventory Net purchases for the month COGS. The formula for this is as follows. Budgeted sales qty x sp.
Another example would be one of your production equipment has broken down so your processes have come to a halt. Its ending work in process is. Has a beginning work in process inventory for the quarter of 10000.
Once youre able to determine your beginning WIP inventory and you calculate your manufacturing costs as well as your cost of manufactured goods you can easily determine how much WIP inventory you have. This beginning inventory equation or opening stock formula is. Work-in-process WIP inventory turns This asset management measure is typically calculated as the cost of goods sold COGS for the year divided by the average on-hand work-in-process material value ie.
This formula can be used to calculate any of the four values given the other three are available. And the result for calculating beginning inventory cost will be as follows. This means that the ending inventory for Bayshore Company is 500 x 1250 6250.
Cost of goods manufactured. Determine the cost of goods sold COGS with the help of your previous accounting periods records. The value of all materials components and subassemblies representing partially completed production at plant cost for the most recently completed fiscal year.
WORK IN PROCESS INITIAL WORK IN PROCESS DIRECT LABOR OVERHEAD - COST OF FINISHED GOODS. 1500 x 20 30000. Once the manufacturer starts the production process those items are no longer raw materials.
Let us take a company ABC which manufactures widgets. ABC International has beginning WIP of 5000 incurs manufacturing costs of 29000 during the month and records 30000 for the cost of goods manufactured during the month. Additionally items that are considered work in progress may depreciate or face a lower demand from consumers once they have been completed.
44000 30000 14000. Ending WIP Beginning WIP Materials in Direct Labor Overheads - COGM Ending WIP 25000 40000 10000 5000 - 45000 Ending WIP 35000. The ending work in process is now calculated using the work in process inventory formula as follows.
COGS Previous accounting period beginning inventory previous accounting period purchases previous accounting period ending inventory. How to Calculate Ending Work In Process Inventory. That is how to find beginning inventory.
Work in process inventory AKA work in progress or WIP inventory is everything that happens to inventory in between raw materials and finished goods. The conceptual explanation for this is that raw materials work-in-progress and finished goods current assets are turned into revenue. As a result of this you would have to freeze the production process until you have bought the materials to use.
The work in process formula is. Its been moved out of its initial warehousing environment and is now a work in progress. 5000 Beginning WIP 29000 Manufacturing costs - 30000 cost of goods manufactured.
The work in process formula is the beginning work in process amount plus manufacturing costs minus the cost of manufactured goods. Ending inventory Previous accounting period beginning inventory Net. 4000 Ending WIP.
Under this method the cost of completed units is calculated by multiplying production expressed in terms of equivalent units. Beginning Inventory Formula COGS Ending Inventory Purchases. Multiply your ending inventory balance by the production cost of each inventory item.
So 1000 x 10 1000 x 15 2000 units 1250. Work in process operating inventory goods in process raw materials used during the period direct labor during the period factory overhead for a period ending inventory. The weighted-average cost method takes the weighted average of all units in the companys inventory.
It is generally considered a manufacturing best practice to minimize the amount of work-in-process in the production area. Lets use a best coffee roaster as an example. The work in process inventory refers to the part of the production cycle of turning your individual raw materials into a kettle.
Abnormal loss- Physical units produced are multiplied by the degree of completion. Opening Inventory Formula. Do the same with the amount of new inventory.
Ending WIP Inventory Beginning WIP Inventory Manufacturing Costs - Cost of Finished Goods. Work in process inventory examples. The work in process formula is.
Next multiply your ending inventory balance with how much it costs to produce each item and do that same with the. But if you already know the beginning inventory and ending inventory figures you can also use them to determine the cost of goods sold. Opening work-in-process inventory closing work-in-process inventory cost of goods manufactured.
This results in a simple calculation to find opening inventory. Therefore the direct labour and the operational cost of putting the kettle together would be classified under work in. The WIP figure reflects only the value of those products in some intermediate production stage.
Work In Process Inventory. Work in process inventory formula. Calculating your beginning inventory can be done in four easy steps.
Abnormal gain- Physical units 100 complete. Higher sales and thus higher cost of goods sold leads to draining the inventory account. Ending Inventory Beginning Balance Purchases Cost of Goods Sold.
Every dollar invested in unsold inventory represents risk.
Cost Of Goods Manufactured Formula Examples With Excel Template
Finished Goods Inventory How To Calculate Finished Goods Inventory
Formula To Calculate Inventory Turns Inventory Turnover Rate
All You Need To Know About Wip Inventory
Ending Inventory Formula Step By Step Calculation Examples
Work In Process Wip Inventory Youtube
Manufacturing Account Format Double Entry Bookkeeping
What Is Work In Process Wip Inventory How To Calculate It Ware2go
Wip Inventory Definition Examples Of Work In Progress Inventory
How To Calculate Ending Inventory The Complete Guide Unleashed Software
Inventory Raw Materials Work In Progress And Finished Goods
Inventory Formula Inventory Calculator Excel Template
Compute The Cost Of A Job Using Job Order Costing Principles Of Accounting Volume 2 Managerial Accounting
Finished Goods Inventory How To Calculate Finished Goods Inventory
How To Calculate Finished Goods Inventory
3 Types Of Inventory Raw Materials Wip And Finished Goods Youtube
How To Calculate Ending Inventory Using Absorption Costing Online Accounting
Ending Inventory Formula Calculator Excel Template